Shandong Denso: Optimizing Tool Cutting Angles for Enhanced Product Performance
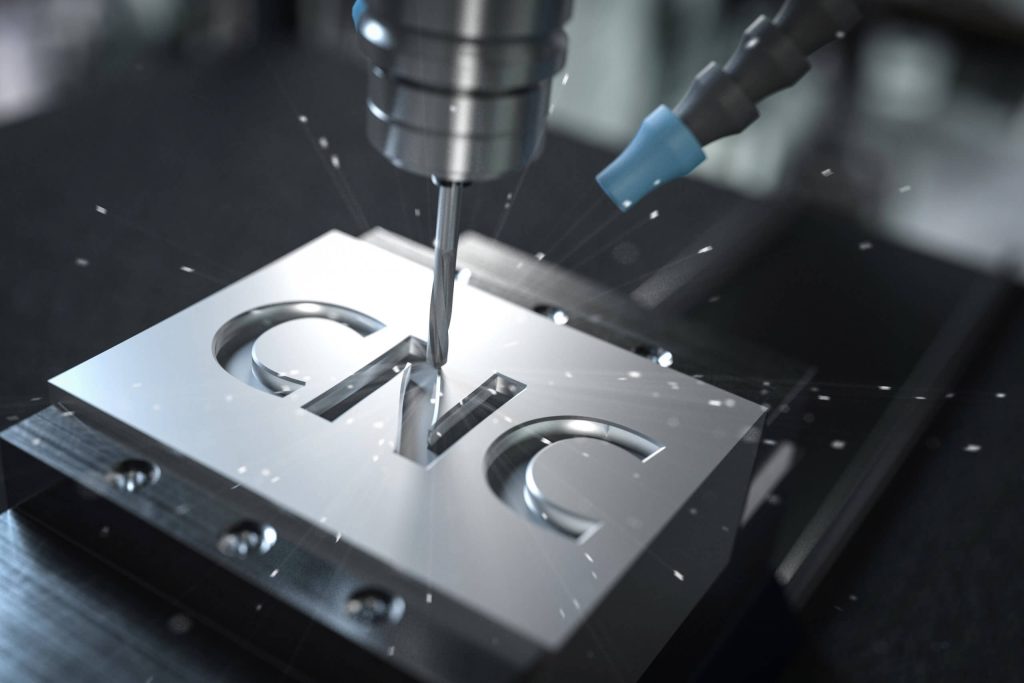
Confronted with the challenge of elevating product performance and lowering production costs, Shandong Denso opted to optimize tool cutting angles. The company adopted a systematic research and experimental approach, selecting representative products as research subjects and conducting multiple machining trials in real-world production settings. During the experiments, they compared two sets of cutting angles: Angle A, representing conventional cutting angles, and Angle B, denoting newly optimized cutting angles.
Impact of Tool Cutting Angles
Tool cutting angles are among the decisive factors governing the interaction between tools and workpieces during the machining process.
The correct choice of cutting angles can effectively reduce cutting forces, enhance cutting efficiency, and directly influence the surface quality of the machined parts.
However, varying materials and machining requirements necessitate different cutting angles, demanding careful selection and adjustment in the production process to achieve optimal machining outcomes.
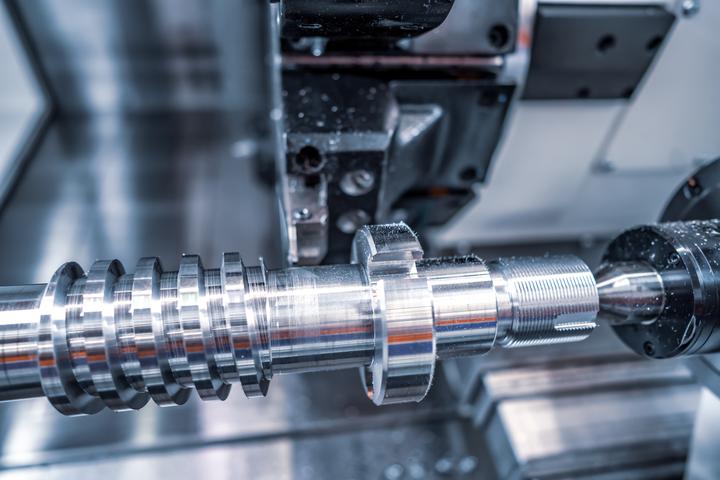
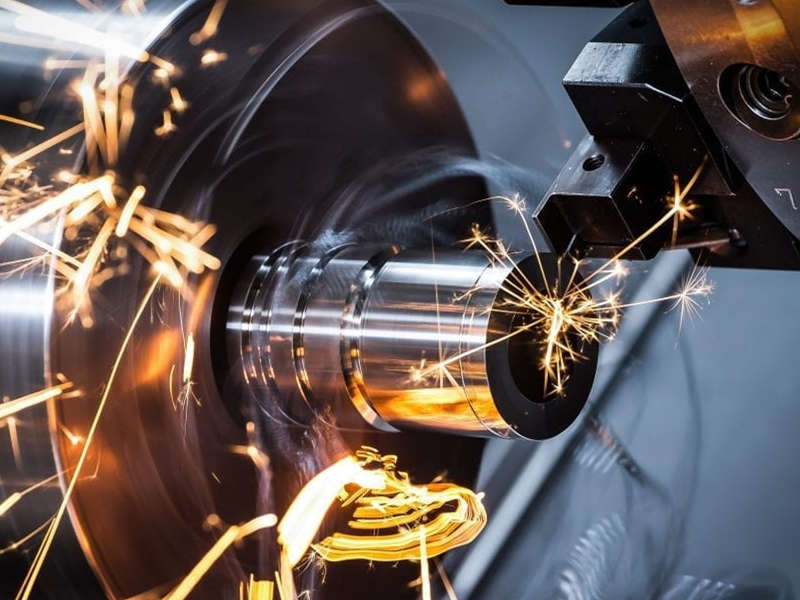
Shandong Denso‘s Exploration and Practice
Confronted with the challenge of elevating product performance and lowering production costs, Shandong Denso opted to optimize tool cutting angles.
The company adopted a systematic research and experimental approach, selecting representative products as research subjects and conducting multiple machining trials in real-world production settings.
During the experiments, they compared two sets of cutting angles: Angle A, representing conventional cutting angles, and Angle B, denoting newly optimized cutting angles.
Through data analysis, researchers scrutinized the machining data under both Angle A and Angle B conditions.
The results revealed that, under Angle B, the average surface smoothness of products improved by 18%, and dimensional accuracy increased by 15%. Simultaneously, Angle B yielded a 10% reduction in cutting forces and an 8% decrease in energy consumption.
These data vividly demonstrated the positive impact of optimizing cutting angles on product performance and production efficiency.
Optimized Outcomes and Future Prospects
By analyzing and comparing the data, Shandong Denso successfully identified the most suitable tool cutting angles for their products and production processes, subsequently implementing the optimized approach in their actual production.
This effort resulted in a 12-20% performance enhancement for their products, not only bolstering market competitiveness but also effectively reducing production costs.
This success story provides valuable insights and references for other manufacturing enterprises seeking to optimize their machining processes.
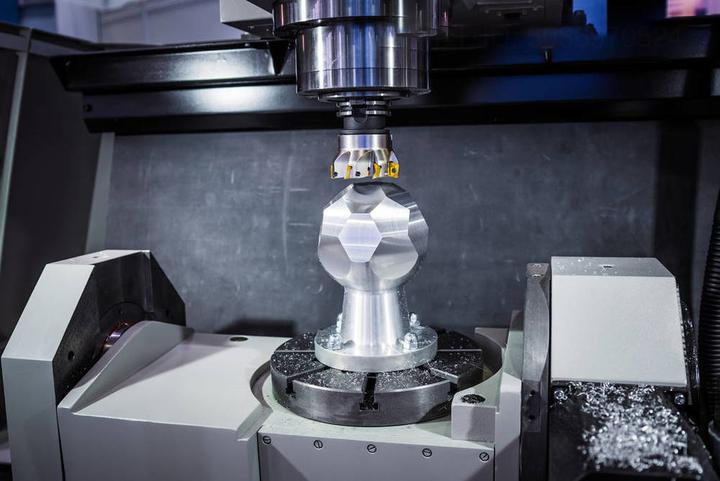
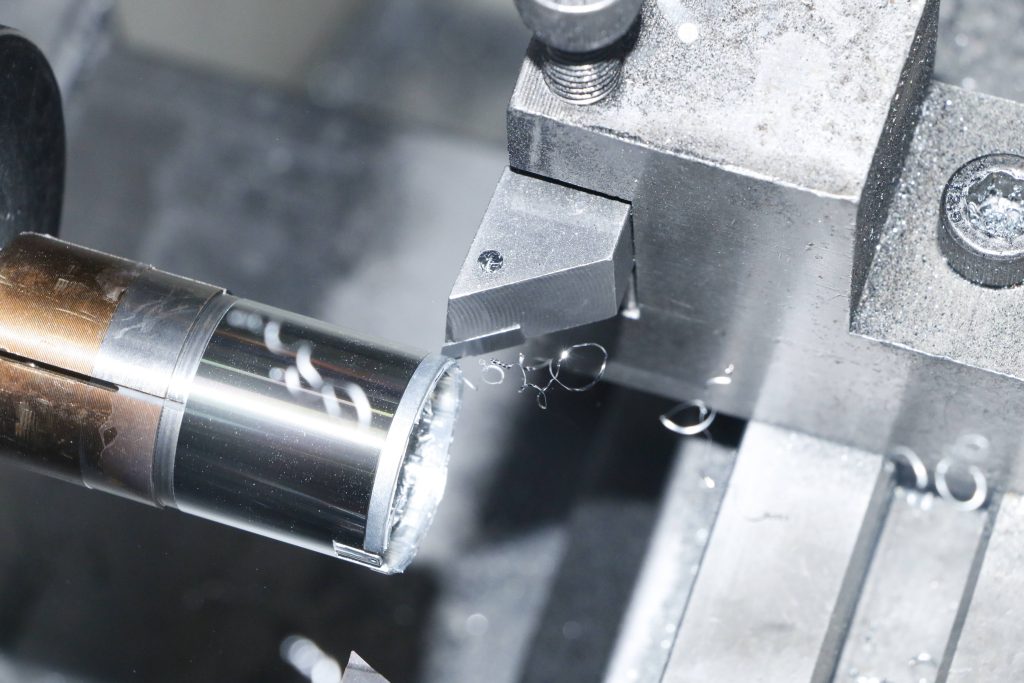
Looking Ahead and Challenges
However, optimizing tool cutting angles is not a one-size-fits-all process.
In practical applications, different materials, machining methods, and product characteristics require comprehensive consideration, necessitating refined research and adjustment.
Moreover, evolving technologies offer new possibilities for optimizing tool cutting angles, such as leveraging advanced simulation software and data analysis tools for decision-making and applying artificial intelligence algorithms for optimization.
Conclusion
This paper delved into the case study of Shandong Denso, demonstrating how optimizing tool cutting angles contributed to a remarkable 12-20% enhancement in product performance.
Through the comparison and analysis of experimental data, the substantial improvements resulting from optimization were clearly evident.
This successful endeavor not only yielded tangible benefits for Shandong Denso but also provided valuable insights for the broader manufacturing industry, offering fresh perspectives for sustaining competitiveness in a fiercely competitive market.
As technology continues to evolve, there is every reason to believe that the optimization of tool cutting angles will continue to play a pivotal role in manufacturing, infusing new vigor into the pursuit of sustainable development for businesses.
About Us
We have been engaged in precision manufacturing since 2000, and we are committed to personnel training, product development, technology development and equipment renewal, steadily growing into one of the outstanding companies in China for precision tools.
Address
- Tel: 0539-4687610
- Skype:(+1)2134255500
- E-mail:eva@densotool.com
- WhatsAPP:(+1)2134255500
- Telegram: https://t.me/densotoolsoem
- Address: Taihe Road, Dongcheng Development Zone, Pingyi County, Linyi City, Shandong Province,China