Types of milling cutters: A comprehensive overview
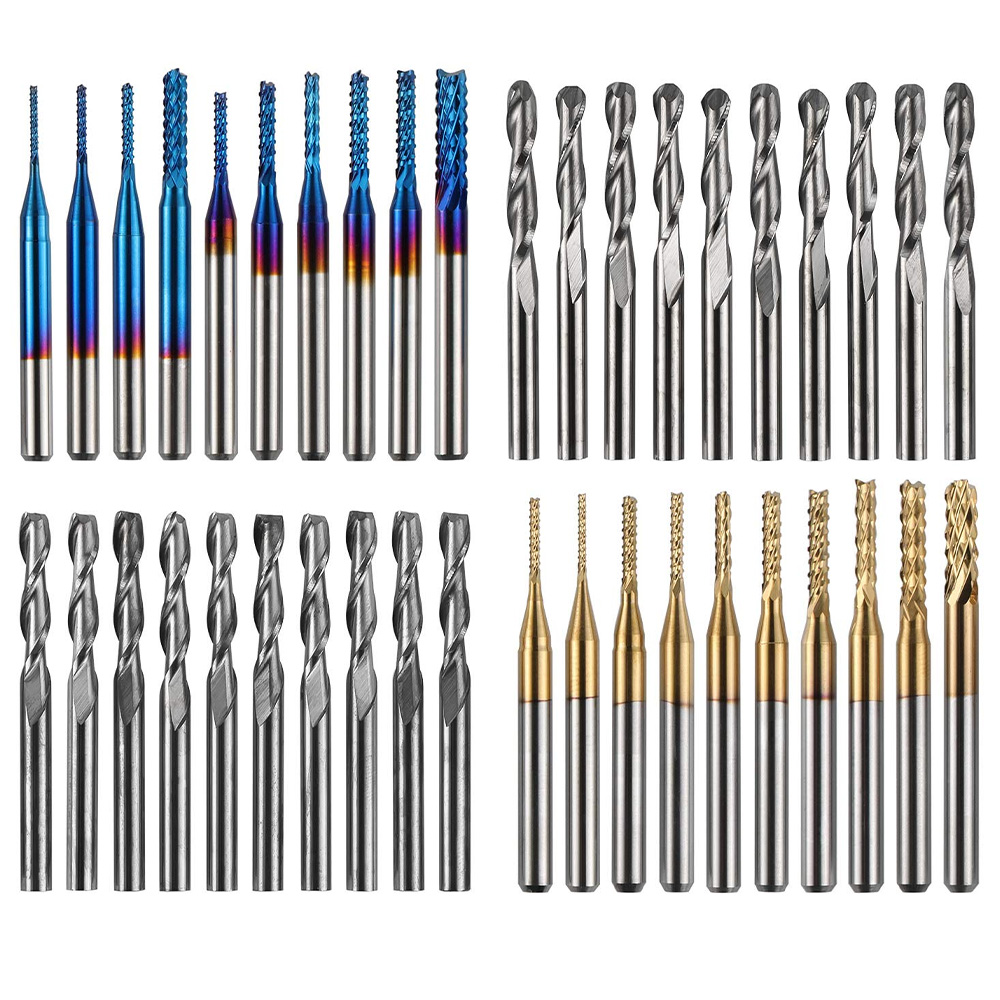
Milling cutters are the basic tools used in machining operations to remove material from workpieces. They come in a variety of shapes, sizes and configurations to suit different cutting requirements. In this article, we will explore the common classifications of milling cutters, outlining their characteristics and applications.
Orientation of milling cutter teeth:
Milling cutters can be classified according to the orientation of their cutter teeth. There are two main types:
a) Straight tooth milling cutters: As the name suggests, these milling cutters have straight teeth parallel to the cutter shaft. They are suitable for general milling operations and are commonly used for a variety of applications.
b) Helical tooth milling cutters: Helical tooth milling cutters are characterised by the teeth being set at an angle to the cutter shaft. This design helps reduce chatter and provides a smoother cutting action, making them ideal for high-speed machining and heavy-duty applications.
Tooth back form:
Another criterion for classifying milling cutters is based on the form of the tooth back, which determines the shape of the back edge of the cutter. The two common types are
a) Sharp-toothed milling cutters: These cutters have sharp teeth for aggressive cutting and effective chip evacuation. They are usually used for roughing operations and for materials that are easy to machine.
b) Spade tooth milling cutters: Spade tooth milling cutters have a more rounded tooth profile, providing better tool strength and durability. They are suitable for machining hard materials and achieving smoother surface finishes.
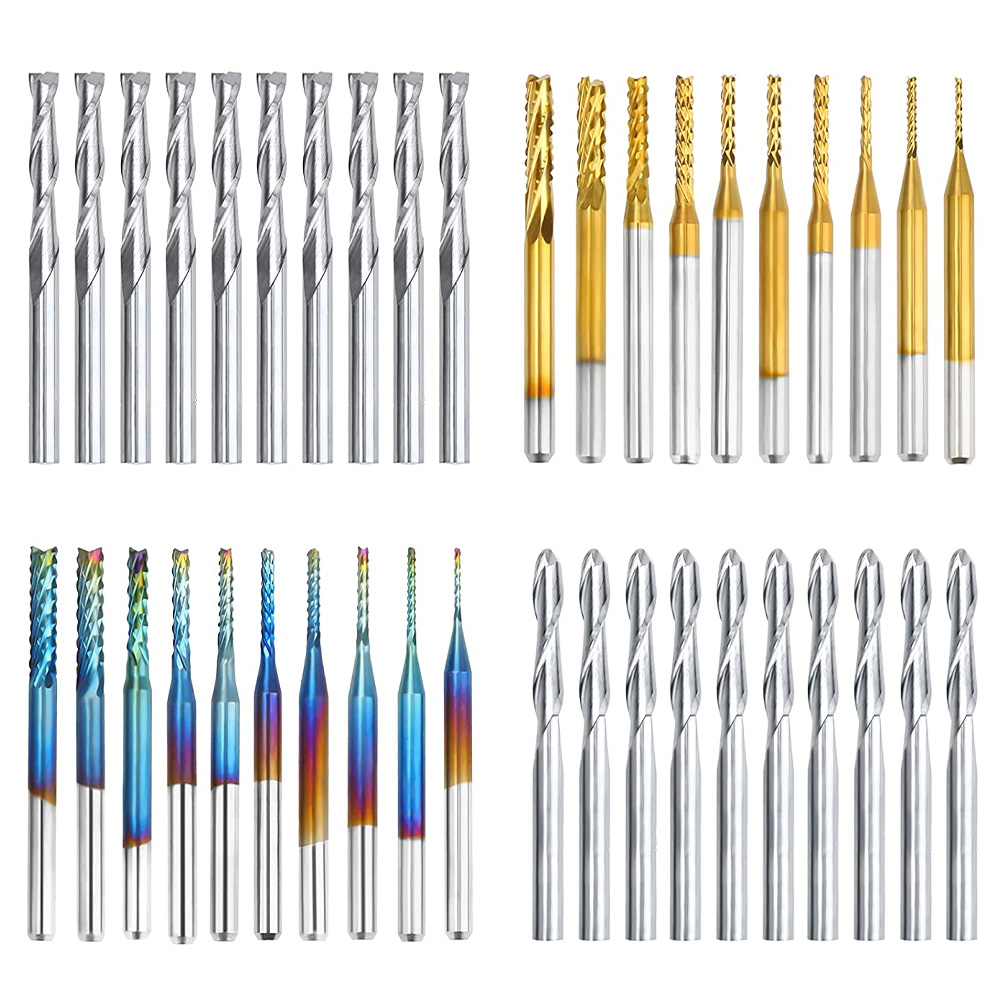
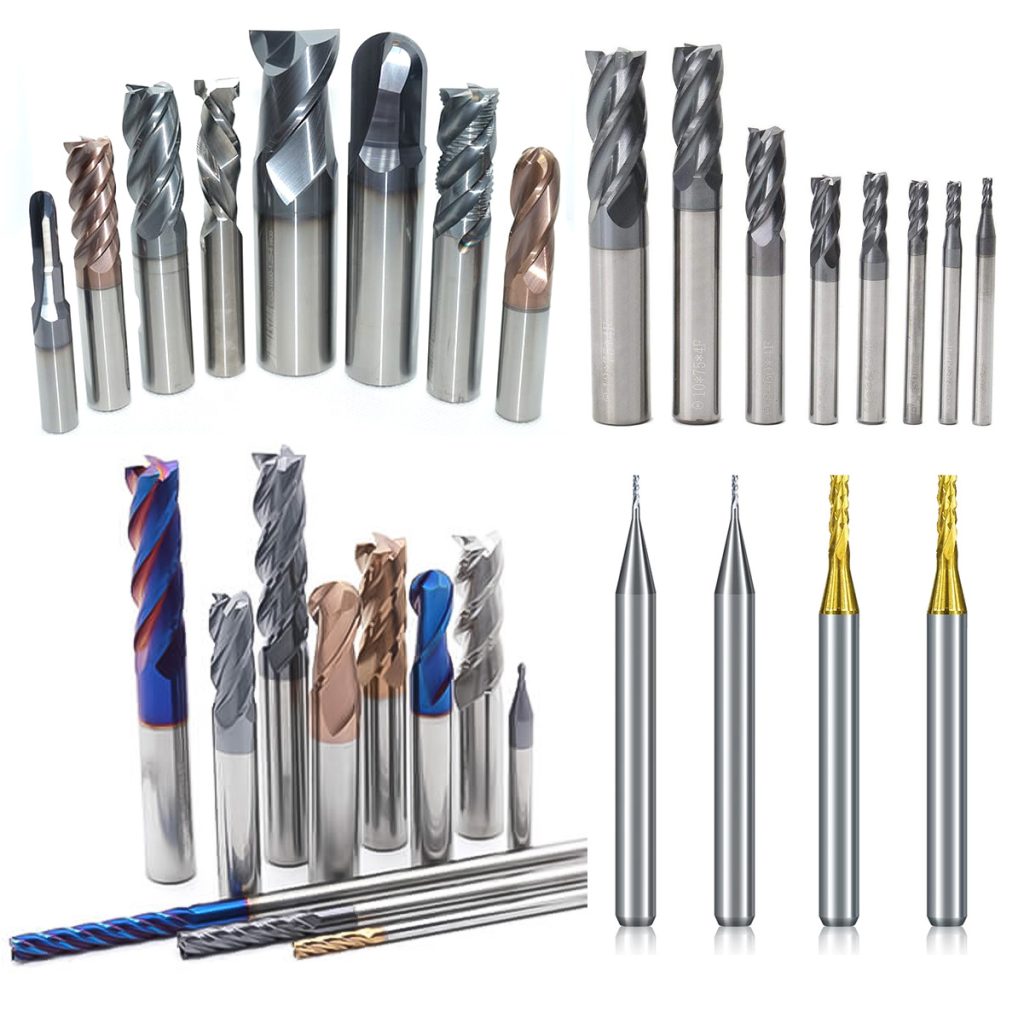
Construction:
Milling cutters can also be classified according to their construction. Here there are four main types:
a) Integral: Integral milling cutters are made from a single piece of material and therefore have a robust construction. They are usually used for heavy-duty milling applications.
b) Welded: Welded milling cutters consist of a cutting edge welded to the body or shank of the cutter. This type allows customisation and flexibility in terms of tool design.
c) Drop-in: Drop-in milling cutters feature replaceable inserts with cutting edges. This design makes maintenance cost effective as only the insert needs to be replaced in the event of wear or damage.
d) Indexable: Indexable milling cutters have multiple cutting edges, usually in the form of inserts. They are versatile and cost effective as worn or damaged cutting edges can easily be replaced or transferred to a new position.
Uses:
Milling cutters can be further classified according to their specific use. The following are some common types:
a) Cylindrical milling cutters: These cutters have peripheral teeth on a cylindrical surface and are used for milling slots, grooves and other similar features.
b) Face milling cutters: Face milling cutters have cutting edges on both the circumference and the end face and are suitable for machining the flat surfaces of workpieces.
c) Disc milling cutters: This type of milling cutter has multiple peripheral teeth on a flat disc and is used for efficient and precise machining of large surfaces.
d) Saw blade cutters: These cutters are similar to saw blades and are used for slotting and cutting operations.
e) Keyway milling cutters: Keyway milling cutters are used to create keyways, i.e. slots to accommodate keys or other similar components.
f) Angle milling cutters: Angle milling cutters are characterised by the cutting edge being at an angle to the cutter axis, allowing chamfering or angular work to be carried out.
g) Forming cutters: Forming cutters are used to create complex contours and shapes on workpieces.
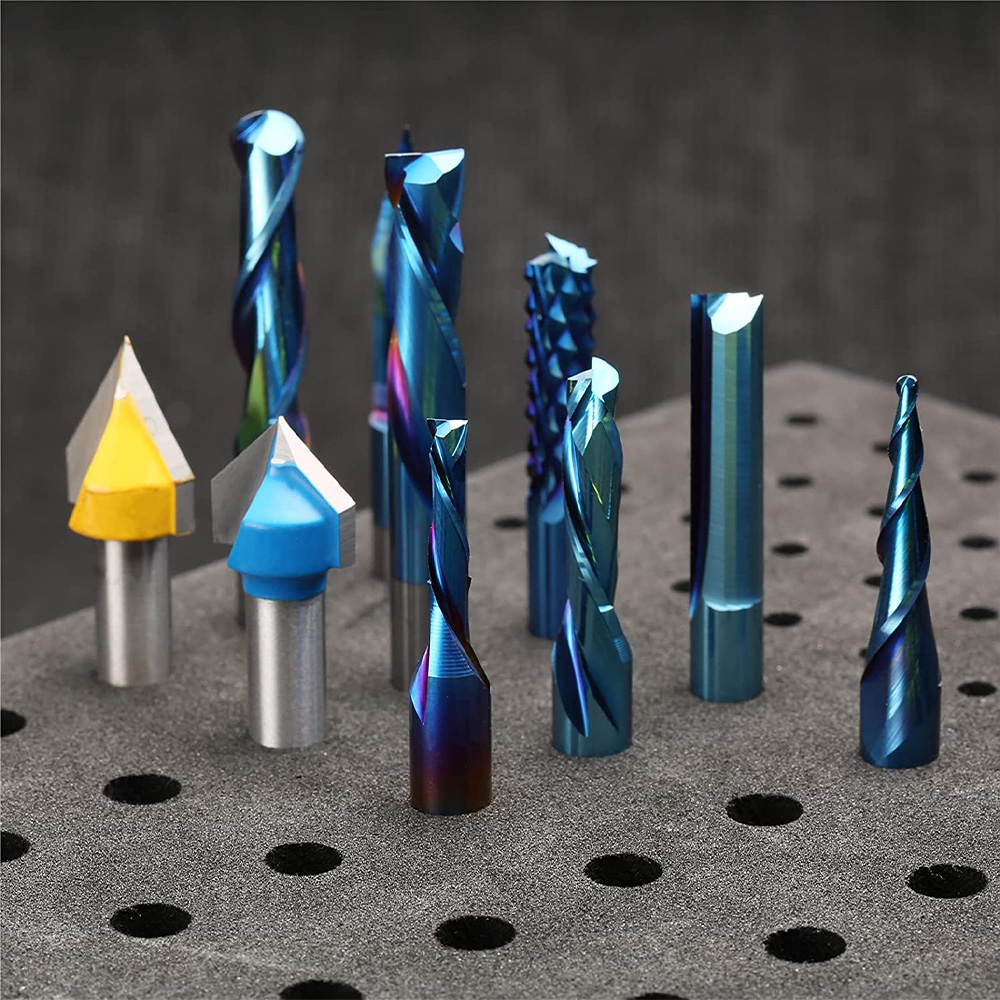
In summary, there are various types and configurations of milling cutters, each suitable for a specific machining task. Understanding the different classifications of milling cutters and their applications can help professionals and enthusiasts alike to select the right tool for their milling operations, ensuring efficient and precise results.
About Us
We have been engaged in precision manufacturing since 2000, and we are committed to personnel training, product development, technology development and equipment renewal, steadily growing into one of the outstanding companies in China for precision tools.
Address
- E-mail:eva@densotool.com
- Tel: 0539-4687610
- Skype:(+1)2134255500
- WhatsAPP:(+1)2134255500
- Telegram: https://t.me/densotoolsoem
- Address: Taihe Road, Dongcheng Development Zone, Pingyi County, Linyi City, Shandong Province,China