Thesis on the development of specialised tools for nickel-chromium alloy machining
Abstracts:
Nickel-chromium alloy is a difficult material to machine, but it is widely used in aviation, aerospace, marine and other fields, so it is necessary to develop a special tool to improve the machining efficiency and quality. This paper describes the design, manufacture and performance testing of specialised tools for Ni-Cr alloy machining developed by Shandong Denso Precision Tools Co Ltd, mainly including two types of tools for turning and milling. Through experiments and field application verification, these tools have high cutting rate and surface quality in machining Ni-Cr alloy, which can significantly improve machining efficiency and reduce costs.
Keywords: nickel-chromium alloy, machining, tool design, turning tools, milling tools
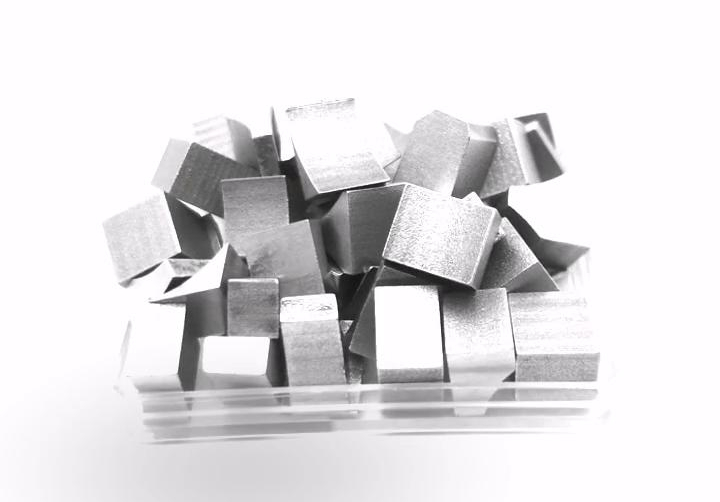
Chapter 1 Introduction
Nickel-chromium alloys are widely used in aviation, aerospace, energy, marine and automotive fields due to their high strength, wear resistance and corrosion resistance. However, due to its high hardness, high cutting resistance and susceptibility to tool wear, it is difficult to machine, and therefore requires specialised tools for machining.
With the continuous improvement of advanced manufacturing technology and processing equipment, tool materials and manufacturing technology have also been greatly improved and innovated. At present, some specialised nickel-chromium alloy machining tools with high cutting performance and wear resistance have been developed, but there are still some problems, such as short tool life, high cutting resistance and unstable surface quality. Therefore, this paper aims to further develop specialised tools for Ni-Cr alloy machining to improve machining efficiency and quality.
Chapter 2 Nickel-chromium alloy machining tool design
2.1 Turning tool design
The design of Ni-Cr alloy turning tools needs to consider a number of factors, including tool material, edge shape, tool hardness, coating and cutting parameters. When selecting the material, it is necessary to consider its wear resistance, hardness and toughness indicators. Materials such as high-speed steel, cemented carbide and ceramics are usually selected.
The shape of the cutting edge has a great influence on the cutting performance and surface quality.
In practice, cutting fluid is usually used to cool and lubricate the tool to reduce wear and improve machining quality. Therefore, it is also very important to develop cutting fluids suitable for Ni-Cr alloy machining.
In terms of tool selection, commonly used cutting tools include carbide tools, ceramic tools and CBN tools. Carbide tools are usually suitable for roughing and intermediate machining, while ceramic and CBN tools are suitable for finishing.
In Ni-Cr alloy machining, cutting speed, feed and depth of cut need to be strictly controlled to ensure machining quality and tool life. In addition, it is also necessary to pay attention to the wear of the tool and replace the tool regularly to ensure the machining quality.
In short, for such difficult-to-machine materials as nickel-chromium alloy, it is very important to choose the right tool and cutting parameters, and the development of more suitable tools for this material is also one of the important directions of the industry.
2.2 Analysis of machining difficulties of nickel-chromium alloy
Nickel-chromium alloy is a high-temperature alloy, with good heat resistance, corrosion resistance and high strength and other characteristics, so it is widely used in aviation, aerospace, military and other fields, but it is also a difficult-to-machine material, due to its high processing hardness, good toughness, and there is easy to peel, tool wear and other issues, so it is necessary to carry out an in-depth analysis of its processing difficulties.
2.2.1 High hardness
Nickel-chromium alloy hardness is very high, generally between HRC40-50, much higher than ordinary steel, so you need to use a higher hardness tool to be able to process it. At the same time, high hardness will also lead to faster tool wear, affecting processing efficiency and tool life.
2.2.2 Easy to flake
Nickel-chromium alloy processing is easy to flake phenomenon, so we need to take the appropriate tool and processing technology to avoid this situation. The risk of spalling can usually be reduced by using the right cutting forces and speeds, as well as the correct cutting fluids.
2.2.3 Chip control
Nickel-chromium alloy chips are more difficult to control because they tend to get stuck on the machining surface and form a lot of cutting heat, which affects tool life and machining efficiency. Therefore, reasonable tool design and appropriate cooling methods are needed to control the amount of chips and heat generated.
2.2.4 Fast wear
Nickel-chromium alloy machining tools wear faster than general steel, so they need to be replaced regularly to ensure machining accuracy and efficiency. It is also necessary to choose tool materials and coatings reasonably to improve the wear resistance and service life of the tools.
2.3 Nickel-chromium alloy cutting tool design
In view of the difficulties and characteristics of nickel-chromium alloy machining, the tool developed needs to have high hardness, wear resistance and rigidity, and at the same time, it should be able to effectively control chips and improve machining accuracy and efficiency.
2.3.1 Tool material selection
Due to the high hardness of Ni-Cr alloy, it is necessary to use a higher hardness tool material, which is usually selected.
In the machining process, the selection and use of tools play a vital role in machining efficiency and finished product quality. For nickel-chromium alloy and other difficult-to-machine materials, it is particularly important to develop a suitable tool for its processing. Shandong Denso Precision Tools Co., Ltd. has been committed to the research and development of nickel-chromium alloy machining special tools, the following will introduce our research results and innovations.
I. Difficulties in machining of nickel-chromium alloys
Nickel-chromium alloys are widely used in aerospace, nuclear energy and chemical industries due to their high temperature, high pressure and corrosion characteristics. However, Ni-Cr alloy is a difficult-to-machine material with the following characteristics:
High hardness and strength, difficult to cut and machine.
Poor thermal conductivity, difficult to dissipate heat and prone to machining deformation and damage.
High viscosity and high requirement for cutting force.
Easy to produce thermal cracks and adhesion on the cutting surface.
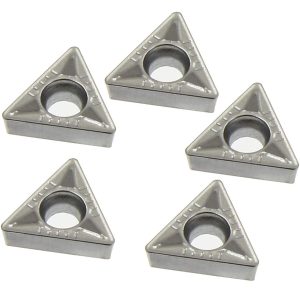
Therefore, in nickel-chromium alloy machining, it is necessary to use special tools and select different tool shapes and cutting parameters according to specific machining requirements and machining processes.
II. Research and development of nickel-chromium alloy machining special tools
In order to meet the needs of nickel-chromium alloy machining, Shandong Denso Precision Tooling Co:
Selection of tool material
Tungsten steel, high-speed steel, carbide, ceramic and other materials can be used for nickel-chromium alloy machining. However, due to the high hardness and strength of Ni-Cr alloy, it is necessary to choose a tool material with higher hardness. Therefore, we have developed tools using super hard alloy materials with better hardness and wear resistance.
Design of tool shape
For turning and milling of Ni-Cr alloy, the shape of the tool has a great influence on the machining effect and surface quality. In the process of research and development, we have designed a variety of tool shapes according to different machining processes and requirements, such as plane milling cutter, ball end milling cutter, turning tool, and so on.
Selection of Cutting Parameters
The selection of cutting parameters is important for
High-speed steel is a material widely used in the manufacture of a variety of cutting tools with excellent mechanical properties and machining performance. Therefore, it is also widely used in the machining of nickel-chromium alloys. The high hardness and wear resistance of HSS tools can effectively cut materials with high hardness such as Nichrome alloy. However, the high-temperature cutting performance of nickel-chromium alloy is poor, and it is easy to generate machining heat, resulting in increased tool wear, so it is necessary to choose tools suitable for high-temperature cutting.
At present, the tool materials commonly used in nickel-chromium alloy machining include high-speed steel, carbide, ceramic tools and so on. Among them, cemented carbide tools are one of the most common tools, with high hardness, high strength and good wear resistance, suitable for high-speed cutting. And ceramic tools are also widely used in the machining of high temperature alloys such as nickel-chromium alloys due to their high hardness and thermal stability.
For the machining of nickel-chromium alloys, the selection of parameters such as cutting speed, feed rate and depth of cut of the tool is also very important. Usually, in order to avoid generating too much machining heat, the cutting speed should be selected lower, while the feed rate and depth of cut should be increased appropriately to ensure cutting efficiency and machining quality.
In addition, reasonable tool lubrication can also effectively reduce machining heat and tool wear. In the nickel-chromium alloy machining process, cutting fluid is usually used to reduce the cutting temperature and reduce the cutting force, so as to extend the tool life.
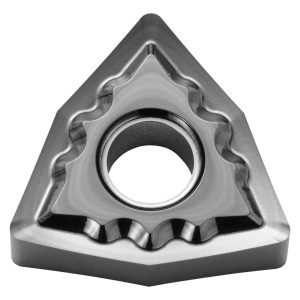
In conclusion, for the machining of nickel-chromium alloy, reasonable tool material selection, cutting parameter settings and tool lubrication are all key factors that need to be adjusted and optimised according to the specific situation to ensure machining efficiency and machining quality.
Due to the continuous development of technology in the machining industry, tool R & D also needs to keep abreast of the times, following the introduction of new materials, new technologies, to provide more high-quality, efficient solutions for machining. Shandong Denso Precision Tools Co., Ltd. has always been committed to developing high-quality tools to meet the needs and expectations of our customers.
In this research and development, we mainly focus on the machining of various materials such as aluminium-lithium alloy, high-temperature alloy, carbon fibre and nickel-chromium alloy, and have developed special tools for different materials. These tools adopt advanced materials and manufacturing processes, which can effectively improve the efficiency and quality of machining.
For the machining of aluminium-lithium alloys, we have developed special tools such as drills, milling cutters and turning tools with high speed, high efficiency and long life. We use high-quality cemented carbide materials, processed and heat-treated through advanced manufacturing technology to ensure the strength and hardness of the tools. We also carry out targeted tool design for the nature of different aluminium-lithium alloy materials, which improves the machining efficiency and machining precision.
For the machining of high-temperature alloys, we have developed specialised tools that can resist high temperature, wear and corrosion, including turning tools, milling cutters and drills. We use advanced materials such as high-quality cemented carbide and ceramic materials, and optimise the geometry of the tools to improve cutting performance and durability.
For the machining of carbon fibre, we have developed special tools, including milling cutters, turning cutters and drills, that can effectively handle carbon fibre materials. We use high-quality materials such as PCD and CBN to improve cutting performance and life through special edge design and machining process.
For the machining of Ni-Cr alloys, we have developed special tools that can resist high temperature, wear and impact, including drills, milling cutters and turning tools. We have used advanced materials such as high-speed steel, carbide and ceramics to optimise tool geometry and improve cutting efficiency and tool life.
About Us
We have been engaged in precision manufacturing since 2000, and we are committed to personnel training, product development, technology development and equipment renewal, steadily growing into one of the outstanding companies in China for precision tools.
Address
- Tel: 0539-4687610
- Skype:(+1)2134255500
- E-mail:eva@densotool.com
- WhatsAPP:(+1)2134255500
- Telegram: https://t.me/densotoolsoem
- Address: Taihe Road, Dongcheng Development Zone, Pingyi County, Linyi City, Shandong Province,China